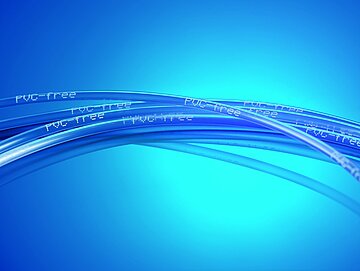
- Material Development
- Interview
- Reading time: 6 min
The important role of PVC in medical devices and applications
Medical device manufacturers look closely at materials like PVC intended for use before starting the development period. In the plastics segment, polyvinyl chloride, or PVC, has been the choice for many medical devices and applications. But today, there is also a growing focus on other materials. The market is demanding alternatives. Dr. Ralf Ziembinski, Head of Product Development Compounds & Extrusions at Raumedic, discusses the given possibilities with us and explains the unbroken demand of medical grade PVC.
Dr. Ralf Ziembinski, Head of Product Development Compounds & Extrusions at Raumedic The important role of PVC in medical devices
Definition: What is medical grade PVC?
PVC stands for Polyvinylchloride. It´s a polymer which consists mainly of chlorine. The addition of plasticizers makes the plastic PVC soft and flexible. This is one of the most desirable properties for medical products.
Why is the usage of PVC in medical devices increasingly the subject of criticism?
This is where we have to make a strict distinction. In the field of medical technology, the criticism is largely aimed at the plasticizers in the material PVC. It has been proven that DEHP or DOP exhibit reproductive toxic characteristics and can be comparatively easily dissolved out of the material. At Raumedic we have used Phthalat-free and DEHP-free plasticizers, such as noDOP (TEHTM), for years to rule out this risk. The probability of migration is minimized by the factor 100 with this substance.
The EU Commission is also taking action: The present exemption that permits the now discredited phthalate for blood bags and transfusion tubes will only be valid until the final sunset date in 2025, when Appendix XIV of the REACH regulation comes into effect.
What speaks for the use of PVC in medical devices?
There certainly are many arguments. Especially for medical-grade plastic disposable products. Medical grade PVC is cost-effective, it is suitable for secondary processing and it has been proven for decades. While materials such as glass and rubber were used in the early days of medical technology, PVC has contributed to make healthcare better and safer. As long as it is DEHP-free medical grade quality, the material is also highly tissue and blood compatible.
The fact that PVC parts and components can also be excellently sterilized before use is also extremely important in the clinical environment. After all, no one wants to risk infections caused by germs.
Will PVC continue to play a decisive role for future medical and pharmaceutical applications ?
This is primarily a question of cost. If alternative materials with similar pricing and comparable properties become established on the market, it could be more likely to rely on them. Otherwise, there would be a greater burden on the healthcare system.
But we believe that PVC will continue to have a certain right to exist in the medical and pharmaceutical industry. Its qualities and technical factors along with its low cost can simply not be dismissed.
Benefits of medical grade PVC are:
- Biocompatibility
- Sterilization capability
- Flexibility
- Transparency
- Material strength
Which ingredients are incompatible with PVC?
If PVC comes into direct contact with medications, any interactions must be carefully checked in advance. There are indeed some active ingredients, including taxol, nitroglycerin, diazepam and insulin, that are incompatible with PVC.
The problem has two facets: First, additives in the drug solutions can cause plasticizers to leach out of the PVC material. Secondly, certain active pharmaceutical ingredients are deposited on the PVC surface. This adsorption is then accompanied by undesirable losses of active ingredients, i.e. a lower dosage.
The rising demand for medical grade alternatives to PVC
More and more customers are already asking us about PVC alternatives, which is often driven by the requirements of hospitals. I think this trend is likely to intensify. But a complete transition to PVC-free materials in medical devices would be a lengthy process, in my view. The manufacturers and the market would have to expect higher costs for alternative materials.
What are alternatives to medical grade PVC ?
There are a few options. For the development of a new drip chamber, for example, we used TPE. For medical tubing, we can offer soft PP, especially when optimum drug compatibility is required. This is because polypropylene - like polyurethane, by the way - does not contain plasticizers. In addition, the material properties are very similar to those of PVC.
If a more cost-efficient alternative to medical grade PVC is sought, coextrusion could be a solution. In this area, we have developed a medical-grade two-layer tubing made from EVA and styrene-butadiene rubber (SBR). Since the outer layer can be equipped with UV-absorbing pigments, it can also be used to optimally administer light-sensitive drugs, such as chemotherapeutic substances. Thanks to the transparent inner layer, the active ingredient does not come into contact with the color pigment. The outer tubing layer made of SBR can also be easily bonded, which plays a major role in further processing.
For which medical devices or applications are these PVC alternatives particularly suitable?
There are many. Our Coex tubing made of EVA and SBR and the TPE drip chamber are ideal for gravity infusion sets and enteral administration sets. For example, when nutrition solutions or drugs are administered parenterally or in enteral feeding. These PVC-free medical grade materials could also be used in the field of transfusion. Soft-PP, in turn, is well suited to replace PVC tubing in infusion pumps.
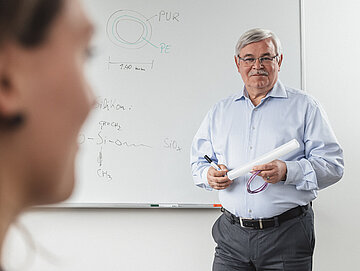
Dr. Ralf Ziembinski
Dr. Ralf Ziembinski is Head of Product Development Compounds & Extrusions at Raumedic. With a doctorate in chemistry, he specialized in the research of inorganic polymers as far back as his post-doc studies at the University of Toronto, before bringing his know-how to RAUMEDIC beginning in 2004.