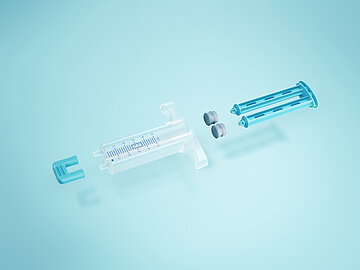
- Development
- Article
- Reading time: 12 min
The “Ready-to-Fill” dual chamber syringe - For precise and safe tissue adhesive application
RAUMEDIC has developed and manufactured an innovative and high-precision dual chamber syringe for a customer. The prefillable system is used in wound surgery and contains two highly viscous components of a tissue adhesive. “Highly viscous” means that the liquids in the syringe are particularly thick to ensure precise handling when dosing during application in the operating room.
The innovative syringe system is a primary packaging material in accordance with ISO 15378 and therefore offers the highest safety and quality standards. Certification in accordance with the primary packaging standard offers the customer a reliable, standard-compliant system for GMP-compliant production for demanding applications.
A particular advantage is that the syringe is supplied as a “ready to fill” solution, which enables aseptic filling under sterile conditions.
Use of the double-chamber syringe in surgery: for improved wound healing and fixation
The double-chamber syringe is used as a supportive measure when conventional surgical procedures reach their limits. It enables the precise delivery of two highly viscous components that act as tissue adhesives and offer the following advantages:
- Improved hemostasis: By locally sealing bleeding sites, blood loss can be reduced.
- Wound healing and sealing of sutures: Particularly in vascular surgery and in the gastrointestinal tract, the adhesive helps to close wounds and support healing processes.
- Tissue bonding: Whether for fixing skin grafts or for bonding subcutaneous tissue in plastic, reconstructive and burn surgery - the tissue adhesive ensures secure and permanent adhesion.
- Replacement for sutures: In certain cases, conventional sutures or staples can be completely replaced by the tissue adhesive, thereby reducing the risk of complications.
Furthermore, the double-chamber syringe is also suitable for additional support of hemostasis on subcutaneous tissue surfaces. It thus enables versatile application in the surgical environment and helps to simplify treatment procedures.
More than just an ordinary contract manufacturer
RAUMEDIC as a reliable development and production partner for a double-chamber syringe for the highest demands
A long-standing customer from the healthcare sector required an ergonomically improved dual-chamber syringe system for highly viscous media. RAUMEDIC, experienced in the development and production of customer-specific syringe systems, made several adjustments: optimized stoppers with special material combinations, a specially designed cap to prevent interactions between material and media and a suitable packaging concept for aseptic filling.
With comprehensive life cycle management and optimized camera and siliconization technology, RAUMEDIC's design-for-manufacturing approach ensured efficiency, compliance with standards and reliable processes.
Let us now take a step-by-step look at how RAUMEDIC, as a developer and manufacturer of double-chamber syringes, led the project to success.
1. First steps and development order
RAUMEDIC was commissioned to develop an improved syringe system that would meet the highest requirements in terms of ergonomics and process reliability. The existing double-chamber syringe required high application forces due to the highly viscous media, which had a negative impact on handling. In addition, the design was to be modernized and the syringe was to be filled from below.
The scope of the project ranged from the initial molded part concept to the design freeze, including the development of the mold concepts. RAUMEDIC took over the complete coordination of the development process so that the customer benefited from a central interface and did not have to coordinate with several partners.
2. Conception & development of the double chamber syringe
In this phase, RAUMEDIC concentrated on the optimal coordination of material selection, geometry and process design. Due to the highly viscous media, special requirements applied to the stability, handling and ergonomics of the entire application system. The aim was to reduce piston actuation forces and ensure precise dosing - without compromising functionality.
Comprehensive material tests and prototype validations enabled targeted optimization of the components. At the same time, RAUMEDIC developed a packaging concept specially tailored to the application to support aseptic filling. The final product design was defined with the design freeze so that implementation in toolmaking and the subsequent validation processes could begin.
3. Special toolmaking & production optimization
Once the design phase was complete, implementation began. RAUMEDIC started with the search for and coordination with specialized toolmakers. Together with the customer, a toolmaker was selected, and the construction of the injection molds could begin. The small cylinder distance and the complex component geometry required the use of innovative tool technologies. Standard solutions proved to be insufficient, which is why a specially adapted tool technology was developed to meet the high requirements for precision and production quality.
The components were designed both in accordance with the agreed standards and functionally so that they could be seamlessly integrated into existing production processes. The manufacturing technologies used and the experience of RAUMEDIC's process and production experts ensured the consistently high quality of the double-chamber syringes produced - while at the same time improving the efficiency of the production processes.
4. Optimization of the double-chamber syringe: stopper & plunger actuation force
A key objective was to reduce the plunger actuation force required for the application. The previous system had high resistance due to the highly viscous media, which made it difficult to use. To improve this, RAUMEDIC initiated an independent development project to optimize the stoppers and their material combinations.
In the course of the project, four material options for the syringe body and 14 different variants for the plunger stoppers were tested. The final material combination achieved lower frictional forces while ensuring a stable connection between the plunger rod and stopper. This improved handling considerably and application forces were significantly reduced.
5. Adaptation of the filling technology & cleanroom packaging of the double-chamber syringe
The switch to filling from below placed special demands on the stopper. This had to be both appropriate for secure pull-up and designed with optimum sliding properties for the application. RAUMEDIC developed a stopper design that met these requirements and enabled smooth processing.
The packaging concept was also revised. An existing standard solution (tub-nest) was adapted to create a customer-specific variant. A tub-nest is a packaging system in which syringes are fixed in a protective plastic holder (“nest”) and stored in a sterile plastic container (“tub”) to enable contamination-free handling.
Tub-nest packaging system
The nest system developed by RAUMEDIC optimized aseptic filling and ensured that the syringes could be introduced into the production line in a stable and low-contamination manner.
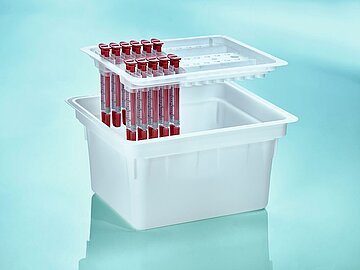
6. Improvement of production processes & quality assurance of the double-chamber syringe
In order to further optimize process reliability, RAUMEDIC implemented targeted measures on the production line.
- Siliconization station: The standardization of siliconization for different syringe sizes reduced the set-up and adjustment effort. Instead of two separate nozzles, one central nozzle was used for both chambers, ensuring uniform siliconization.
- Cleaning station: An additional cleaning unit was integrated into the production line to ensure the highest standards of cleanliness.
RAUMEDIC also introduced an in-process control to measure the sliding force. This minimized the amount of silicone oil required and avoided interactions with the media contained, which contributed to maximum product safety.
7. Life Cycle Management (LCM) & continuous improvement
RAUMEDIC pursues an active life cycle management approach in order to continuously optimize products and solutions - such as the double-chamber syringe shown here - even after market launch. Changes in regulatory requirements or material availability are identified at an early stage and implemented accordingly.
To ensure the long-term quality and standard compliance of the syringe, RAUMEDIC relies on a structured process that includes the following measures:
- Regular standards review: The Regulatory Affairs department continuously checks standards for updates. Customers are proactively informed in order to implement necessary adjustments at an early stage.
- Material adaptations: If material suppliers make changes to materials, RAUMEDIC works with the customer to develop test packages for validation and supports the regulatory submission.
- Process optimization: Production processes are continuously developed to ensure efficiency and product quality in the long term.
This comprehensive approach ensures that RAUMEDIC not only supplies its customers with an optimized double-chamber syringe but also acts as a reliable development and production partner in the long term.
From the idea to series production - RAUMEDIC as a developer for double-chamber syringes
The successful implementation of the double-chamber syringe shows that RAUMEDIC is much more than a contract manufacturer: it is a development and production partner that supports solutions from the initial idea to series production and beyond.
Thanks to in-depth material expertise, state-of-the-art manufacturing technologies and a forward-looking life cycle management strategy, RAUMEDIC ensures that customized syringe systems meet the highest requirements - today and in the future.
Find out more about RAUMEDIC's expertise in syringe systems
Whether development, production or life cycle management - RAUMEDIC is your partner for high-precision syringe systems that meet the highest quality and safety standards.
Find out more about our solutions for innovative injection systems:
Or contact us directly - we will be happy to advise you on customized solutions for your requirements.